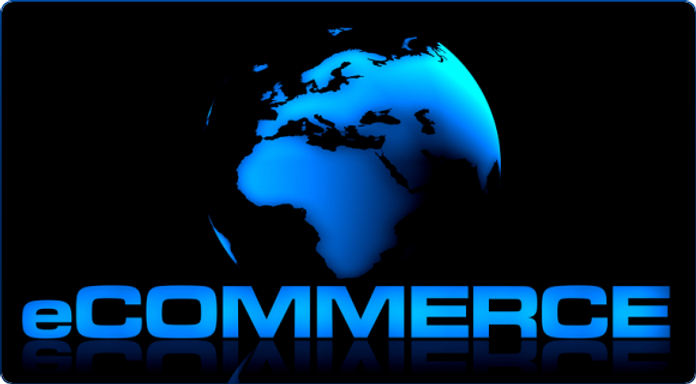
OPERATION MANAGER
An operations manager runs the day-to-day operations of an organization or business. Her sole purpose is to find ways to make the company more productive by providing effective methods in its business operations.
MATERIAL MANAGER
handles all aspects of equipment, raw material and other supplies required to run a company. The position is found in most every company from manufacturing to medical supplies. The manager oversees personnel, inventory, storage space and customer demands. Along with materials, the manager maintains documentation and develops a budget for the department.
PURCHASING MANAGER
who is responsible at some level for buying or approving the acquisition of goods and services needed by the company. The position responsibilities may be the same as that of a buyer or purchasing agent, or may include wider supervisory or managerial responsibilities. A Purchasing Manager may oversee the acquisition of materials needed for production, general supplies for offices and facilities, equipment, or construction contracts. A Purchasing Manager often supervises purchasing agents and buyers, but in small companies the Purchasing Manager may also be the purchasing agent or buyer.
INDUSTRIAL PRODUCTION MANAGER
oversee the daily operations of manufacturing and related plants. They coordinate, plan, and direct the activities used to create a wide range of goods, such as cars, computer equipment, or paper products.
OPERATION RESEARCH ANALYST
are involved in top-level strategizing, planning, and forecasting. They use advanced techniques from mathematics, science, and engineering to make better decisions and to solve problems. These analysts help to allocate resources, measure performance, design production facilities and systems, manage the supply chain, set prices, coordinate transportation and distribution, and analyze large databases. They also have been used in wartime to effectively deploy radar, search for enemy submarines, and get supplies to where they are most needed.
QUALITY ASSURANCE MANAGER
efers to the planned and systematic activities implemented in a quality system so that quality requirements for a product or service will be fulfilled.[1] It is the systematic measurement, comparison with a standard, monitoring of processes and an associated feedback loop that confers error prevention. This can be contrasted with Quality "Control", which is focused on process outputs.
FACILITIES COORDINATOR
s responsible for maintaining the efficient and smooth operation of some type of physical job site. The exact duties of the coordinator may be different, based on the type of business. Most facilities coordinators either work in the hospitality area, an office, or an industrial setting. The education for a facilities coordinator often includes a minimum of an Associate's degree in business, or a similar field.
LOGISTIC MANAGER
oversees the storage and movement of goods and supplies. Logistics managers are relied upon for nearly every aspect of modern life, often without even knowing it. People in this position arrange the movement of raw materials and finished goods. These items go to processors and manufacturers that create everything from electricity to clothing to televisions. Managers also arrange the warehousing of goods and organization of logistics departments.
JOB OPPORTUNITIES: OPERATION MANAGEMENT